Baltimore, Maryland
Resilient Rowhouse Community


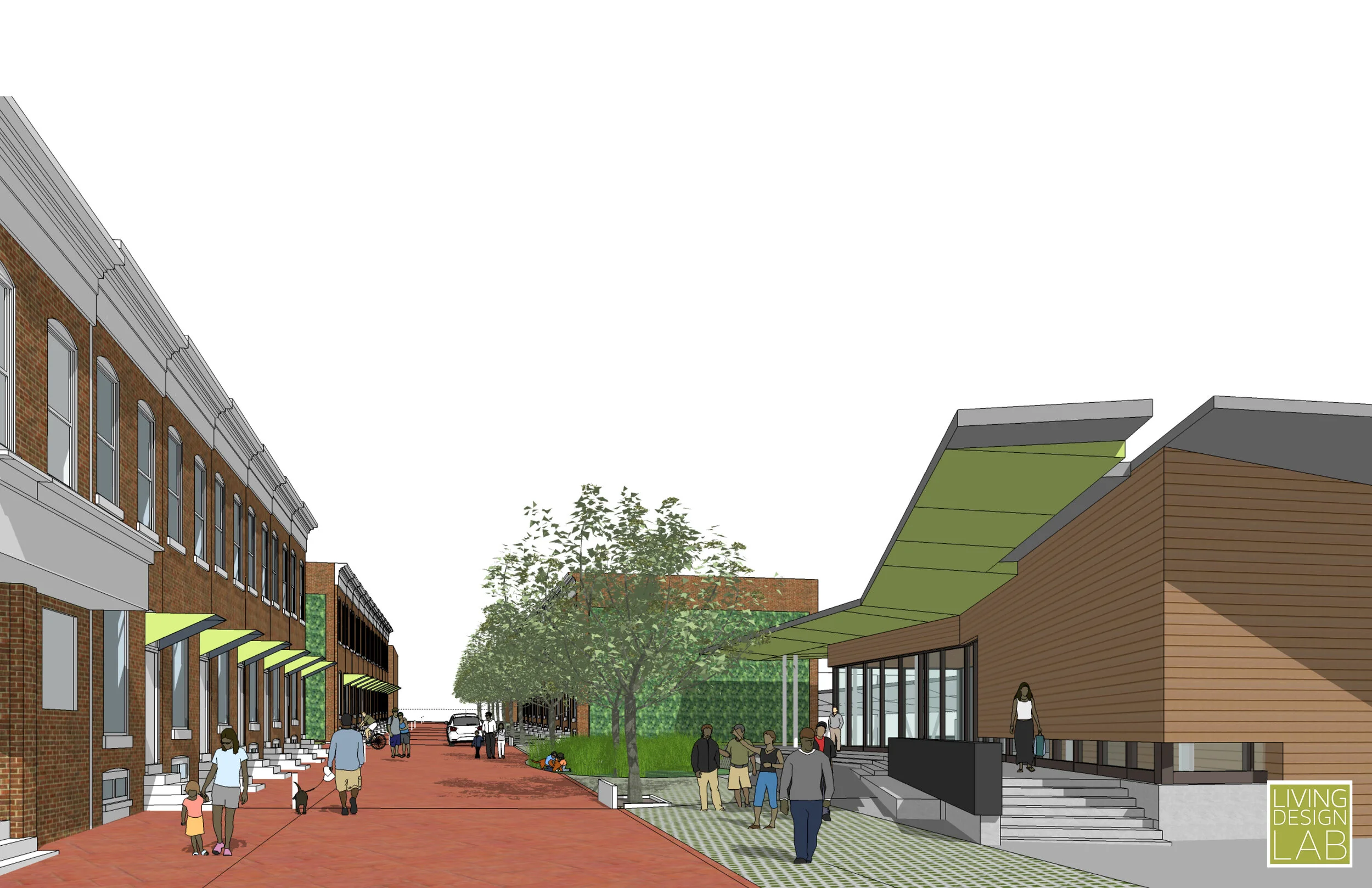
In response to the goals of the competition, the design proposes a cooperative development with a microgrid fuel cell and solar system. In combination with permeable surfacing to mitigate stormwater runoff, the development is designed to weather catastrophic events with little disruption. Additionally the design builds stability in communities as a low-cost home ownership solution. The rowhouses would leverage the “sweat equity” model of Habitat for Humanity, while isolating high skill elements core elements for offsite modular construction. The advantage afforded is high quality, expedient construction with competitive costs.
Truly resilient solutions address social and economic realities in equal measure to the conservation of energy and environment. Any approach to revitalizing Baltimore’s neighborhoods must therefore be holistic, recognizing the complex history of social distress and economic disinvestment that has shaped inner city neighborhoods into what they are today. The high number and concentration of vacant, dilapidated houses in impoverished neighborhoods are merely symptomatic of greater societal failings. The restoration of these hardest hit areas of the city will depend on strategic interventions that support and strengthen the welfare of families. Yet the physical reconstruction of neighborhoods can also powerfully affect social outcomes by establishing a sense-of-place and a sense of ownership.
The approach to the “Resilient Rowhouse” considers the complexity of issues at play in Baltimore’s inner city neighborhoods. The design strategy seeks to build not only sustainable buildings and sites, but also sustainable communities through workforce development, cooperative ownership and through the creation of social spaces.
It is important to understand housing as a community of people living together. In order to foster a sense of community, the selective demolition of rowhouses is used to create porosity between streets and alleys, increasing opportunities for human interaction and access to amenities. These connections lead to the centerpiece of the design: a neighborhood commons building that contains a community “family room” for informal and formal gatherings and an adjacent large “front porch” open for casual use. By reducing backyards, communal parking areas are added along the alleys, paved with porous paving. As such, alleyways are treated as public open spaces, with playgrounds, rain gardens and community gardens. Meanwhile, Prentiss Place is transformed to be a “voonerf”, a street designed to prioritize pedestrians over cars. This narrow street thereby becomes a central public space that encourages socialization between neighbors. Car access is restricted to local traffic and parking is allowed at a temporary basis only for pickup or drop-off. The tree lined pedestrian street incorporates permeable paving with a drainage rill that directs stormwater to a landscaped rain garden in front of the commons building.
The operation of the site is based on the cooperative ownership model. By establishing a cooperative entity, the common areas can be maintained and manned at a central post located inside the commons building. And enabling residents to “own” their neighborhood in a literal sense, increases a sense of responsibility and improves outcomes.
Baltimore has many exemplary organizations and businesses that are working to bring about community revitalization. Habitat for Humanity of the Chesapeake utilizes a volunteer workforce and buyer participation program to build homes at drastically reduced costs. Meanwhile, the Civic Works Baltimore Center for Green Careers develops local workforce by training unskilled youth and adults for green jobs. Through Civic Works’ Energy Ready Initiative, cool roofing would be applied on all low-sloped roofs to build workforce readiness while also reduce energy loss and heat island effect.
William-Scotsman, one of the world’s largest modular building manufacturers is headquartered in Baltimore. In order to further save cost and improve efficiency in construction, we have partnered with William-Scotsman to prefabricate modular core elements. Bathrooms and kitchens would be factory build and erected on site by crane, greatly reducing construction lead times. The approach also strengthens the volunteer based construction model by reducing dependency on skilled trades for on-site work. As Habitat for Humanity reconstructs the shell, William-Scotsman would insert the modular units containing plumbing, power distribution, fixtures, cabinets, appliances and major finishes.
Meanwhile, the building envelope would be super-insulated with low-VOC spray foam insulation on all exterior exposures. Windows would be high performing with low-e glass and insulated units. Additionally, a rooftop cupola would have clerestory lights above the stairs to increase natural daylighting and reduce artificial lighting dependency. The clerestory windows would also be operable to allow for natural ventilation through stack effect.
Next-generation communities must respond to the demand for clean, renewable energy that is both resilient and high-performance. Whereas the State of Maryland has approved a Renewable Portfolio Standard (RPS) that will require the State to generate 30% of its energy from renewables by the Year 2030, our team envisions the redevelopment of Baltimore’s rowhouse communities as being supportive to these renewable energy goals.
Central to the rowhouse energy plan is the development of a Micro-Grid that can generate 100% of the site’s energy demand (net zero performance) while also maintaining the ability to island from the grid when necessary. Energy is generated by fuel cell technology in combination with on-site solar. Solar arrays will be located in the alleys as shade canopies above parking spaces. Meanwhile, fuel cells are located in a central plant located in the commons building. Fuel cell systems can utilize natural gas, hydrogen, methane and bio-gas as their fuel source giving them fuel source flexibility that can be modified depending upon readily available fuel sources. Also, the underground design of the micro-grid infrastructure greatly reduces damage from storms, vehicles accidents and vandalism.
The fuel cells will consistently provide electricity along with a hydronic heat stream that can be piped underground and into the rowhomes for a radiant floor heating system and domestic hot water. Cooling performance within the micro-grid would be done via ductless mini-splits within each housing unit or through a centralized absorption cooling system.
The micro-grid would be developed as a public-private partnership between the City of Baltimore and renewable energy developers. Within the public-private partnership, Urban Green, LLC (a private sector energy developer) would purchase, install, own and operate the site’s fuel cell system, meters and monitoring network. The City of Baltimore would utilize CDBG funds and bond funds to develop and install an underground micro-grid system. The underground micro-grid would be leased to Urban Green on a 10-year ground lease cycle that will allow the City to be repaid for their investment while maintaining long-term ownership of the underground infrastructure.
Davin’s Role: Design Principal
Architect: Living Design Lab
share